很多人會(huì)疑惑,為什么注塑模具的高溫會(huì)產(chǎn)生高光澤的塑件呢?現(xiàn)在我們從兩個(gè)方面來解釋這個(gè)問題。
Many people will wonder why the high temperature of injection mold will produce high gloss plastic parts? Now let's explain this problem from two aspects.
模具溫度對(duì)外觀的影響:
Effect of mold temperature on appearance:
模具溫度過低,熔體流動(dòng)性降低,可能出現(xiàn)欠注現(xiàn)象;模具溫度會(huì)影響塑料的結(jié)晶度。對(duì)于ABS,如果模具溫度過低,產(chǎn)品光潔度就會(huì)低。與塑料和填料相比,塑料在高溫下更容易遷移到表面。
If the mold temperature is too low, the melt fluidity will be reduced, and underinjection may occur; Mold temperature will affect the crystallinity of plastic. For ABS, if the mold temperature is too low, the product finish will be low. Compared with plastics and fillers, plastics are easier to migrate to the surface at high temperatures.
因此,當(dāng)注塑模具溫度較高時(shí),塑料成分更接近注塑模具表面,填充性會(huì)更好,亮度和光澤度也會(huì)更高。但注塑模具的溫度不宜過高。如果過高,容易粘模,塑件部分會(huì)出現(xiàn)明顯的亮點(diǎn)。如果注塑模具溫度過低,也會(huì)造成塑件抱得太緊,脫模時(shí)容易拉傷塑件,尤其是塑件表面的花紋。
Therefore, when the temperature of the injection mold is high, the plastic composition is closer to the surface of the injection mold, the filling property will be better, and the brightness and gloss will be higher. But the temperature of the injection mold should not be too high. If it is too high, it is easy to stick to the mold, and there will be obvious bright spots in the plastic part. If the temperature of the injection mold is too low, it will also cause the plastic parts to be held too tightly, and it is easy to pull the plastic parts during demoulding, especially the patterns on the surface of the plastic parts.
多段注塑可以位置問題。例如,如果產(chǎn)品進(jìn)膠時(shí)有氣紋,可以采用分段注塑的方法。在注塑行業(yè),對(duì)于有光澤的產(chǎn)品,模具溫度越高,產(chǎn)品表面的光澤度越高。相反,如果溫度低,表面的光澤度也較低。但是,對(duì)于陽光紋理PP材料制成的產(chǎn)品,溫度越高,產(chǎn)品表面的光澤度越低。光澤度越低,色差越大,光澤度與色差成反比。
Multi stage injection molding can solve the position problem. For example, if the product has gas lines when it is injected, the method of sectional injection molding can be adopted. In the injection molding industry, for shiny products, the higher the mold temperature, the higher the gloss of the product surface. On the contrary, if the temperature is low, the surface gloss is also low. However, for products made of sun textured PP materials, the higher the temperature, the lower the gloss of the product surface. The lower the gloss, the greater the color difference, and the gloss is inversely proportional to the color difference.
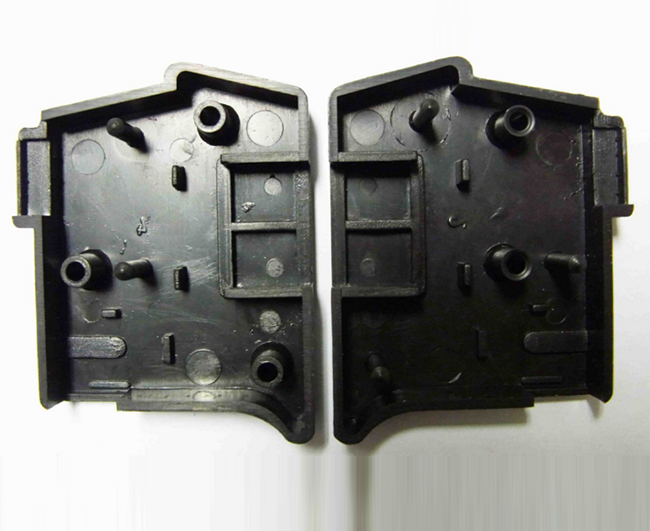
對(duì)產(chǎn)品尺寸的影響:
Impact on product size:
如果模具溫度過高,熔體會(huì)熱分解。產(chǎn)品出來后,空氣中的收縮率會(huì)增加,產(chǎn)品尺寸會(huì)變小。模具在低溫下使用時(shí),如果零件尺寸變大,一般是由于模具表面造成的。溫度過低引起的。這是因?yàn)槟>弑砻鏈囟忍?,制品在空氣中收縮少,所以尺寸要大一些!
If the mold temperature is too high, the melt will be thermally decomposed. After the product comes out, the shrinkage in the air will increase and the product size will become smaller. When the mold is used at low temperature, if the part size becomes larger, it is generally caused by the mold surface. Caused by low temperature. This is because the mold surface temperature is too low, the product shrinks less in the air, so the size should be larger!
原因是:低模溫加速了分子的“凍結(jié)取向”,增加了模腔內(nèi)熔體凍結(jié)層的厚度,同時(shí)低模溫阻礙了晶體的生長(zhǎng),從而降低產(chǎn)品的成型收縮率。反之,模具溫度高時(shí),熔體冷卻慢,松弛時(shí)間長(zhǎng),取向度低,同時(shí)有利于結(jié)晶,制品的實(shí)際收縮率為大的。
The reason is that low mold temperature accelerates the "freezing orientation" of molecules, increases the thickness of the melt freezing layer in the mold cavity, and at the same time, low mold temperature hinders the growth of crystals, thus reducing the forming shrinkage of products. On the contrary, when the mold temperature is high, the melt cooling is slow, the relaxation time is long, the degree of orientation is low, and it is conducive to crystallization. The actual shrinkage of the product is large.
如果在尺寸穩(wěn)定之前啟動(dòng)過程太長(zhǎng),這表明模具溫度沒有很好地控制,因?yàn)槟>咝枰荛L(zhǎng)時(shí)間才能達(dá)到熱平衡。
If the start-up process is too long before the size is stable, it indicates that the mold temperature is not well controlled, because the mold takes a long time to reach thermal equilibrium.
濟(jì)南注塑加工廠家認(rèn)為模具某些部位散熱不均勻會(huì)大大延長(zhǎng)生產(chǎn)周期,從而增加成型成本!恒定的模具溫度減少了成型收縮的波動(dòng)并提高了尺寸穩(wěn)定性。對(duì)于結(jié)晶性塑料,模具溫度高有利于結(jié)晶過程,完全結(jié)晶的塑件在儲(chǔ)存或使用過程中不會(huì)發(fā)生尺寸變化。
Jinan injection molding manufacturers believe that uneven heat dissipation in some parts of the mold will greatly prolong the production cycle, thus increasing the molding cost! Constant die temperature reduces the fluctuation of forming shrinkage and improves dimensional stability. For crystalline plastics, high mold temperature is conducive to the crystallization process, and fully crystallized plastic parts will not change in size during storage or use.
但是,高結(jié)晶度會(huì)導(dǎo)致大的收縮。對(duì)于較軟的塑料,成型時(shí)應(yīng)采用較低的模具溫度,有利于尺寸穩(wěn)定性。對(duì)于任何材料,模具溫度恒定,收縮率一致,有利于提高尺寸精度!
However, high crystallinity will lead to large shrinkage. For softer plastics, lower mold temperature shall be adopted during molding, which is conducive to dimensional stability. For any material, the mold temperature is constant and the shrinkage rate is consistent, which is conducive to improving the dimensional accuracy!
以上是問題答案的相關(guān)內(nèi)容。我希望它可以幫助大家。如果您對(duì)此問題有任何疑問,歡迎您關(guān)注我們的網(wǎng)站
http://www.820hu.com并咨詢我們的工作人員,他們將竭誠(chéng)為您服務(wù)。
The above is the relevant content of the answer to the question. I hope it can help you. If you have any questions about this issue, you are welcome to follow our website http://www.820hu.com And consult our staff, who will serve you wholeheartedly.