濟南注塑加工廠家給大家講解下注塑產(chǎn)品毛刺過多的原因分析,毛刺大多發(fā)生在分型面上,即在動模和靜模之間,滑塊的滑動部分,插入件的間隙,彈出器的孔等,熔體流入熔融材料中,零件上形成多余的飛邊。
Jinan injection molding manufacturer explained to you the cause analysis of too many burrs of injection molding products. Most burrs occur on the parting surface, that is, between the moving die and the static die, the sliding part of the slider, the gap of the insert, the hole of the ejector, etc. the melt flows into the molten material, and redundant flash is formed on the parts.
這樣的毛刺將在成型過程中起到杠桿作用,并將進一步增加毛刺,這將導致模具局部凹陷,并且毛刺將在注射成型過程中進入增加的惡性循環(huán)。因此,如果在開始時發(fā)現(xiàn)毛刺,必須盡快修整模具。
Such burr will act as a lever in the molding process and further increase the burr, which will lead to local depression of the die, and the burr will enter an increasing vicious circle in the injection molding process. Therefore, if burrs are found at the beginning, the die must be trimmed as soon as possible.
出現(xiàn)故障的原因有幾個:
There are several reasons for the failure:
1.鎖模力不足以進行注塑成型
1. The clamping force is insufficient for injection molding
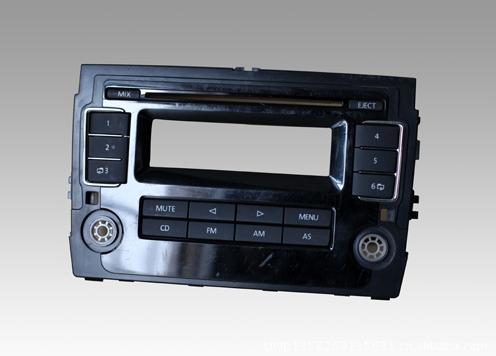
與成型零件的投影面積相比,如果夾緊力較小,則由于注射壓力的緣故,動模和靜模之間會存在間隙,這不可避免地會產(chǎn)生毛刺。特別是當將側(cè)澆口放置在靠近零件中心的孔上時,由于這種成型澆口需要較大的注射壓力,因此非常容易產(chǎn)生毛刺。
Compared with the projected area of molded parts, if the clamping force is small, there will be a gap between the moving die and the static die due to the injection pressure, which will inevitably produce burrs. Especially when the side gate is placed on the hole close to the center of the part, it is very easy to produce burrs because this molding gate requires large injection pressure.
降低注射壓力或增加夾緊力可以這種缺陷。如果根據(jù)具體情況切換到流動性好的低壓成型,有時會非常有效。
This defect can be eliminated by reducing the injection pressure or increasing the clamping force. It is sometimes very effective to switch to low-pressure forming with good fluidity according to specific conditions.
2.注塑模具變形引起
2. Caused by deformation of injection mold
如果模具的原始度不足,則會因注射壓力而偏移。如果中心附近有孔,則孔周圍會產(chǎn)生毛刺。當使用中心孔打開側(cè)門時,也會產(chǎn)生該孔和流道的周邊。毛刺。由于該原因而產(chǎn)生的毛刺是由于不良的模具制造造成的,因此難以修復。加固模具可以減少毛刺。
If the original degree of the mold is insufficient, it will be offset due to the injection pressure. If there is a hole near the center, burrs will be generated around the hole. When the center hole is used to open the side door, the periphery of the hole and runner will also be generated. skin needling. The burr caused by this reason is caused by poor mold manufacturing, so it is difficult to repair. Strengthening the mold can reduce burrs.
3.塑料流動性太好
3. The fluidity of plastics is too good
僅僅是因為塑料的流動性太好,從理論上講并不是毛刺的原因。但是,當塑料的流動性太好時,即使是很小的間隙也可能被塑料穿透,因此容易出現(xiàn)毛刺。為了這種毛刺,可以降低熔融溫度或注射壓力,也可以降低模具溫度或注射速度。
It's just that the fluidity of plastic is too good. In theory, it's not the cause of burr. However, when the fluidity of the plastic is too good, even a small gap may be penetrated by the plastic, so burrs are easy to appear. In order to eliminate such burrs, the melting temperature or injection pressure can be reduced, and the mold temperature or injection speed can also be reduced.
4在注塑過程中過多地注入熔融材料
4 excessive injection of molten material during injection molding
這不是故障的直接原因。為了防止收縮,注入過多的熔融材料是錯誤的。有必要增加成型的注射時間或保持時間(請參閱收縮率)。
This is not the direct cause of the failure. In order to prevent shrinkage, it is wrong to inject too much molten material. It is necessary to increase the injection time or holding time of the molding (see shrinkage).
5.注塑模具表面有異物
5. There are foreign matters on the surface of the injection mold
模具夾緊面上有異物,不可避免地會產(chǎn)生毛刺。為了這個問題,顯然必須清潔干凈模具的表面,以使夾緊表面閉合。
There are foreign matters on the clamping surface of the die, which will inevitably produce burrs. In order to solve this problem, it is obviously necessary to clean the surface of the die to close the clamping surface.
以上就是濟南注塑加工廠家給大家分享的文章,希望對大家有所幫助。
The above is the article shared by Jinan injection molding manufacturer. I hope it will be helpful to you.